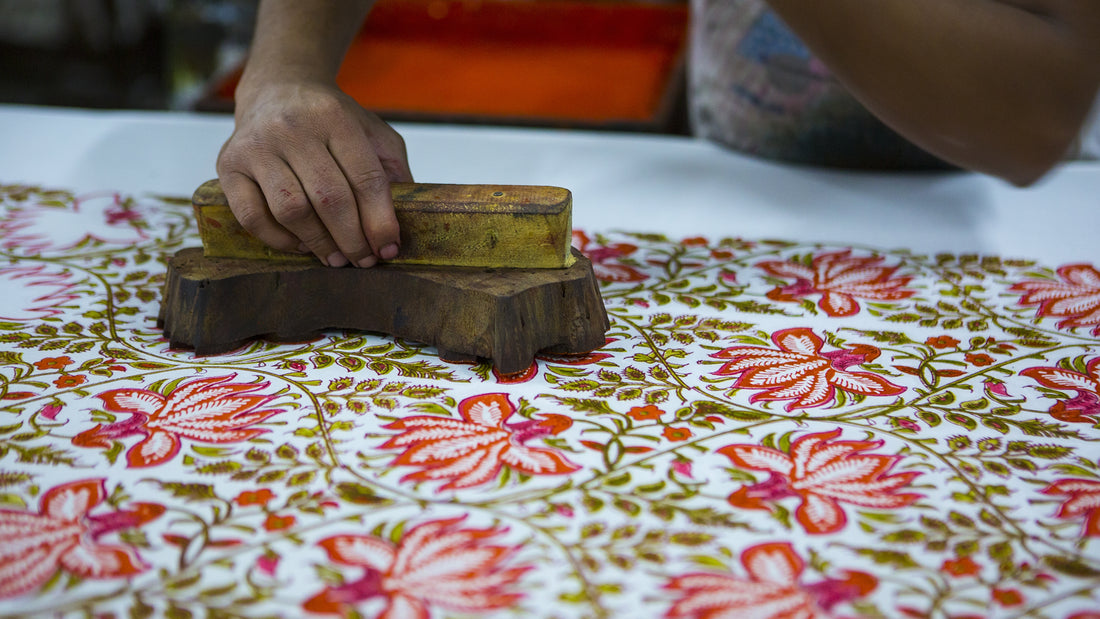
Block Printing In India
What is Block Printing?
Block Printing also known as hand block printing is an ancient technique used to print designs or patterns on textiles using wood blocks and natural dyes. This process is widely practiced in Rajasthan since the 12th Century - back when block prints were considered a symbol of royalty. Block printing in India is most widely found in a small village called Bagru, 30kms from Jaipur in Rajasthan in addition to Sanganer, Barmer, Pali and Jaipur itself. In addition to this, block printing can also be found in other parts of the country such as Gujarat, Uttar Pradesh, Kolkata, Madhya Pradesh and Andhra Pradesh.

Block Printing Process
Block printing requires the use of Blocks - which are used like stamps to imprint the fabric. These blocks are usually of two types: wooden and metallic.
Wooden blocks are hand carved by craftsmen. These are mostly made of teak wood - the treatment of which requires it to be soaked in oil for 10-15 days before it can be carved out for the desired design.
Metallic blocks are made by hammering in thin sheets of beaten metal into designs drawn on the wooden blocks.
Before the printing begins, the fabrics are washed in rivers or other waterbodies to remove starch. Depending on the base colour requirement of the fabric these may be dyed also. They are then let to dry straight under the sun - which is a reason why during the monsoons, the traditional block printing process suffers a setback.
To begin the printing process, the dried fabric is pinned on to a long table so that to ensure that the printing is even and designs don't get smudged. The base dyes used for block printing are usually just 4 or 5 natural colours, which are mixed together to create a large range of dyes.
The blocks are then dipped into the desired dye by the craftsmen and stamped onto the pinned fabric - almost always from left to right on the table. The stamping process requires an element of force applied on it which is usually achieved by either by hitting the stamp with the hand or with a hammer. The fascinating point here is that most of these designs have an outline block and a filling block, which means that these designs would have to be stamped on twice - once for the outline, and then to fill the design.
Once the printing is complete, the fabric is placed to dry under the sun. Once it is dried and steamed, the printed fabric is once again washed and laid out to dry under the sun! Post this comes the ironing!
Types of Block Printing
It is interesting to note that there are three different types of block printing
- Direct Printing: involves directly printing the desired designs on the washed and bleached/dyed fabric by the artisans.
- Resist Printing: in this method, the areas to be protected from the dye are covered using a mixture of clay and resin. The dyed fabric is then washed. On washing, the dye spreads through the cracks, producing a ripped effect. Block prints are then used to further create designs on the fabric.
- Discharge Printing: Here, the fabric is dyed. A chemical is then used to remove the dye from the portions that will be given a different colour. These portions are then treated to be given a different colour.
What makes block printing unique is that it is an ancient & age old technique practiced by many families for generations together; and it is still a form of art providing a livelihood to many families across the country!